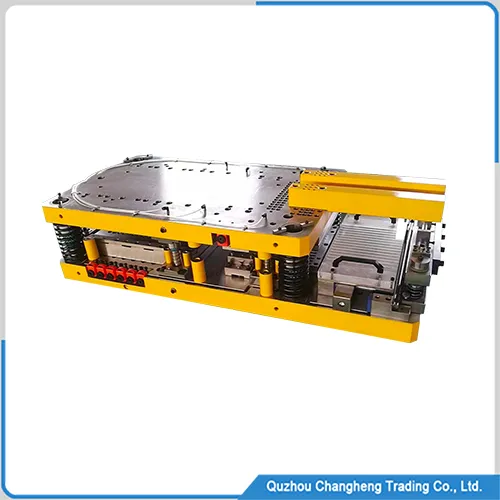
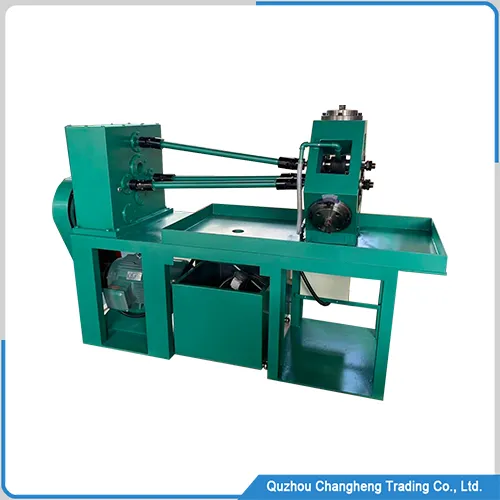
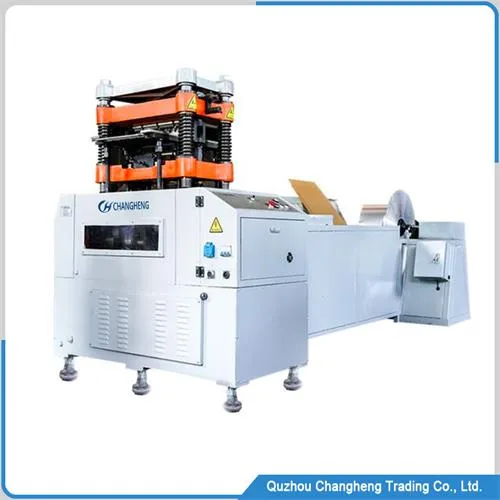
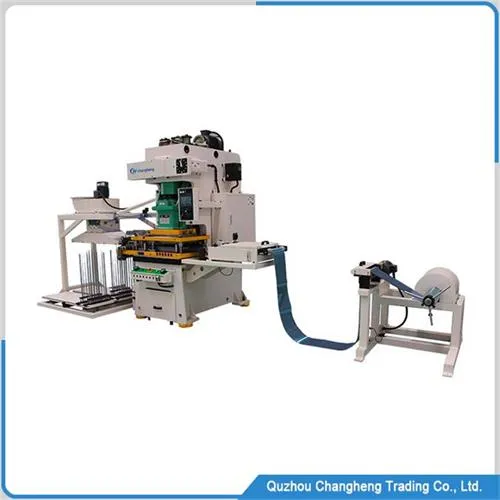
What is a Progressive die?
It is a continuous production automatic mold in modern industrial manufacturing, which consists of multiple units with different functions inside. Each unit completes different tools, such as stretching, bending, trimming, punching, etc. With each stroke of the stamping machine, this Progressive die can produce a complete metal part. It has an efficient production mode and ensures high parts consistency.
The mold production process is fully automatic, without workers needing to participate. The mechanical structure inside the mold completes the addition of lubricant and the step of moving raw materials. It can effectively ensure the dimensional accuracy of parts and output reliable product quality.
Thanks to the high-speed production and smooth output of accurate size and quality of this Progressive die, the application of this mold is pervasive, especially in the HVAC industry, as well as in the industrial cooling industry, etc., all of which cannot do without the participation of this mold.
Progressive Mold features
- Integration of multiple processes
This large mold integrates multiple functional modules inside, such as punching, bending, forming, cutting, etc. Each process completes its own function and realizes high-speed production.
- High-efficiency production
Usually, this Progressive die is connect to the swing arm of the stamping machine, realizing the action of automatic feeding, without workers’ participation. Therefore, it can achieve high-speed production, and the maximum speed can reach 400 times per minute.
- High-precision manufacturing
The upper and lower dies of this Progressive die and the core parts of other small molds are all machined using CNC machines.
The arrangement of each process is based on scientific design, and all parts of the assembled mold are positioned by guide pins. Compared to ordinary molds, its structure is more complex, and its cost is also higher.
- Safety operation
It is a highly integrated mold, with complete automat production, and waste materials are blown out of the mold by compressed air, avoiding operators from contacting dangerous areas. Therefore, users do not need to worry about safety issues.
- Scope of application
This mold is particularly suitable for parts made of thin materials, and for products that need mass-produced, such as the motor rotor, the fins of a heat exchanger, etc. If the size of the product is large and the material thickness is relatively thick, this mold is not suitable.
Design and structure
As an efficient production tool, the design of the progressive die is based on the special characteristics of the parts, allowing each small module to distribute independent functions and forces. This not only improves the production efficiency of the mold but also extends its lifespan.
The shape structure of the mold must have 4 guide columns, and it must have springs that distribute the force evenly. Each small module’s stamping mold must also have guide columns, ensuring the correct guidance of the upper and lower molds and the stability of the size and quality.
Some special molds need to be Install with servo motors to expand the possibilities and shape special shapes and sizes.
One of the prerequisites for designing a mold is to take into account the characteristics of the stamping machine and fully leverage its performance, to achieve the possibility of “1+1 is greater than 2”.
The biggest mistake in designing a mold is creating one with the best performance, but we can’t install it on a stamping machine for production. This is regrettable.
When designing molds, we also need to consider the properties of materials fully. For example, cutting blades must be made of materials such as SKH51 or SKH11, which have high hardness and good wear resistance. Mold and fixing plates raw materials come from EN C45, which is more cost-effective.
For the stability of product quality and the lifespan of molds, the key parts need to be quenched and hardened, which is crucial in every mold manufacturing process. Almost all Progressive dies manufactured by CHANGHENG Company undergo vacuum quenching and are Hardness to 60-62.
More Progressive dies
HVAC fin die for heat exchanger
Product Description This fin die is a core tool in the HVAC industry, designed to meet the requirements of continuous high-speed production. It mainly produces complex fin products stamped from…
Fin press die Manufacturer in China
Press mold Overview As a Chinese manufacturer of fin press dies, we provide customized solutions, design and manufacturing, testing, and maintenance services to meet our customers’ unique needs. Our mold…
Fin progressive die of heat exchanger
Fin mold summarize This type of fin progressive die is a key component in the field of heat exchangers, consisting of multiple independent pressing units to produce a complete fin…
Technical parameters
- Parts hardening technology: Vacuum quenching
- Hardness: 60-62
- Template material: EN C45
- Manufacturing tools: CNC machine tools
- Technical integration: AutoCAD or SolidWorks
- Mold type: fin mold or rotor
- Blade material: SKH51
- Product size: Follow the customer’s design
- Appearance color: Yellow
- Mold brand: CHANGHENG
- Working mode: Fully automatic
- Warranty period: 1 year
- Stamping machine: Any type
Video of a progressive die manufacturer’s factory
The use and precautions of progressive dies
- Before the stamping machine starts working, it is necessary to check that there are no tools, screws, wrenches, calipers, etc. on the mold, because these parts may fall into the mold during high-speed production, causing irreversible damage.
- The guide post position of the mold has an oil tube, which can be connected to the lubrication device of the stamping machine to achieve standardized maintenance and extend the lifespan of the mold.
- The Progressive die manufactured by CHANGHENG uses an independent design for key parts. If there is wear during long-term use, this part can be changed independently at a low cost, ensuring a stable output of dimensions and reducing maintenance costs.
- When the mold needs to change the production size or replace the raw materials, the stamping machine needs to cut off the Power supply for the safety of the work and avoid causing unnecessary injuries.
- If the mold pause use for a long time, it is best to apply a layer of anti-rust oil, and then wrap it with plastic film to prevent the surface of the mold from rusting and getting dusty.