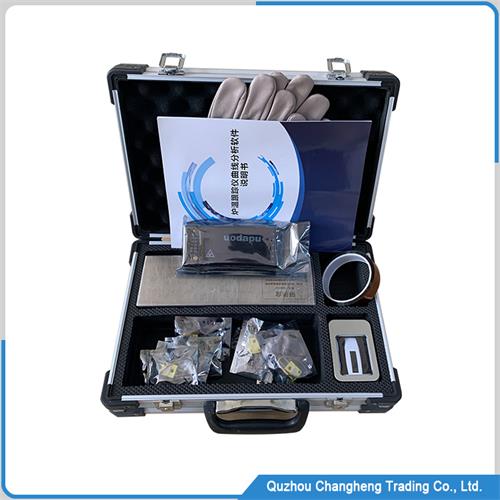
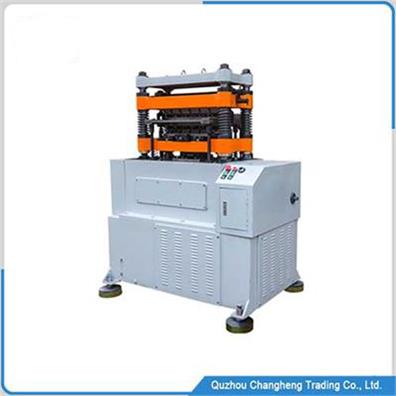
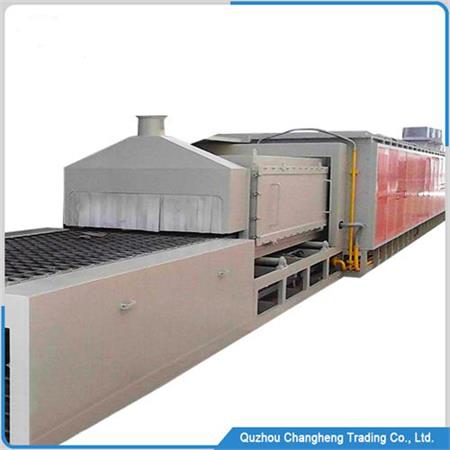
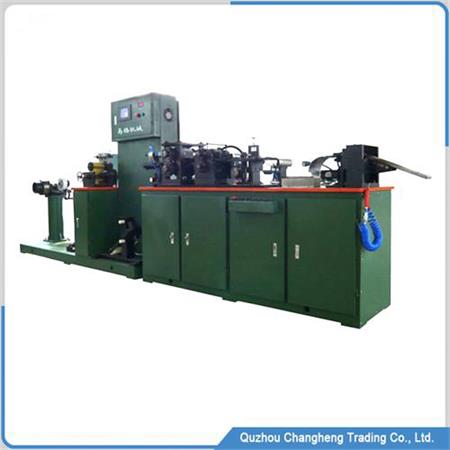
Machine Overview
The Aluminum vacuum brazing oven is a device that uses graphite elements for heating, and its maximum operating temperature can reach 750 ℃. This compact muffle furnace is very suitable for aluminum brazing industrial production and is an ideal equipment for producing plate and bar-type heat exchangers.
Aluminum vacuum brazing oven has the following characteristics and advantages:
- Heating element: Graphite material is used as the heating element, which can provide a stable and uniform heating effect, thereby ensuring high-quality processing and processing of the material.
- Temperature range: The furnace can reach a temperature of up to 750 ℃, which can meet the brazing needs of all aluminum materials.
- Vacuum environment: This vacuum brazing oven has a vacuum function and can perform material treatment in an oxygen-free or inert gas environment, effectively preventing oxidation and pollution of the material surface.
- Compact equipment: The aluminum vacuum brazing furnace is designed to be compact and occupy small space, which can meet the factory’s requirements for equipment volume and space limitations.
Vacuum Brazing Oven Quick Details
No. | ITEM | DATA |
1 | maximum temperature | 750℃ |
2 | Usage | Vacuum aluminum Brazing oven |
3 | Chamber size | Customised |
4 | Working temperature | 650℃ |
5 | Heating Rate | 0-20C/min |
6 | Certificate | CE |
7 | Voltage | 110V/60Hz |
8 | Warranty | One Year |
9 | Heating element | Fe-Mo-Cr sprial wire |
10 | Origin | China |
Vacuum Brazing Oven Features
- 1. Operation Temperature: 700℃ (750℃ for short time).
- 2. Maximum energy efficiency is achieved by surrounding the chamber with thermal-efficient alumina fiber ceramic insulation.
- 3. Heavy duty double layer structure with cooling fan. Lower temperature in outside case.
- 4. PID automatic control via current limiting phase angle fired the resistor, e.g. SCR (Silicon Controlled Rectifier).
- 5. Power control with 51 segments programmable
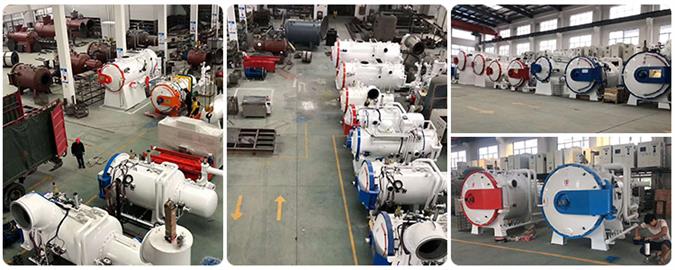
A: The delivery time of our vacuum furnaces is 95 days, and that of some customized vacuum furnaces is 120 days
A: Our vacuum furnace chamber size is customized according to customer requirements
A: Our vacuum packaging is wooden cases, and some large-sized furnaces are packed with plastic film, Because of the packing in wooden cases, it may not fit into containers smoothly
A: Our after-sales service includes installation of machines, technical training and free delivery of easily damaged parts.