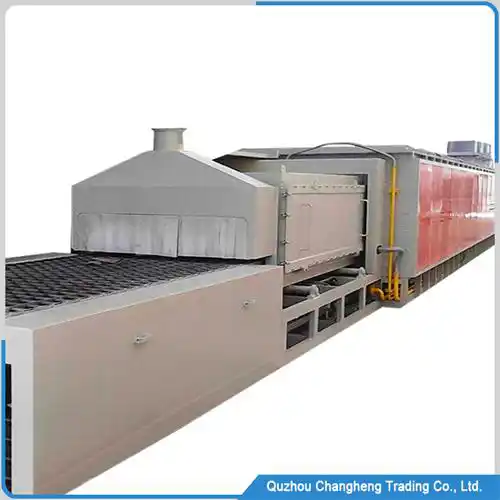
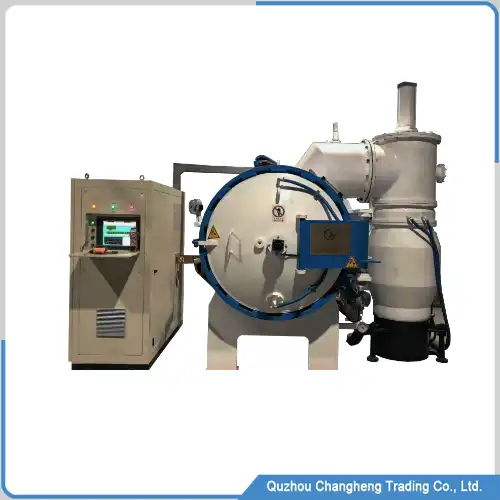
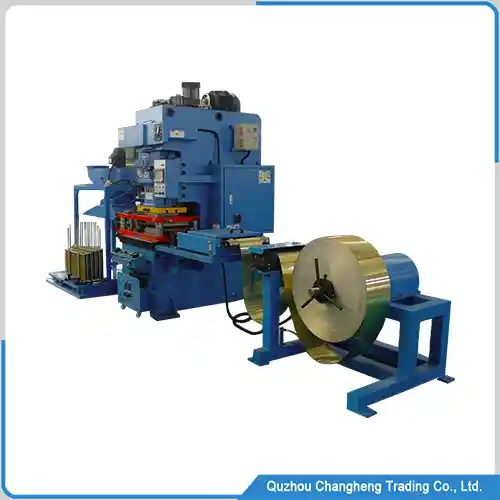
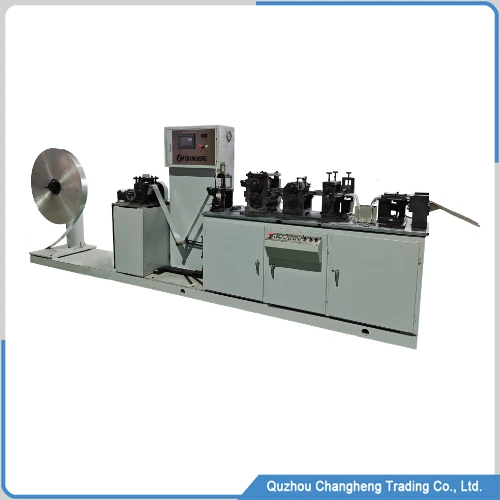
Machine Overview
The continuous brazing furnace is an efficient and automated aluminum radiator production equipment. Its working process involves brazing in a nitrogen-protected atmosphere, which effectively avoids oxidation issues on the surface of the aluminum core, ensuring welding quality and production efficiency.
In addition, it can achieve continuous and uninterrupted production, greatly improving production efficiency.
Overall, the continuous brazing furnace is an ideal choice for the production of aluminum radiators, and its high efficiency, automation, and continuous production capacity have brought significant production benefits to enterprises.
The characteristics of the continuous brazing furnace
1, Efficient production:
The continuous brazing furnace adopts a continuous production method, which can achieve uninterrupted production, reduce production costs, and improve production efficiency.
2, Automation control:
This equipment is equipped with an advanced automation control system, which can achieve automated temperature control, and ensure the stability and consistency of the production process.
3, Accurate parameter setting:
The continuous brazing furnace can set precise parameters such as temperature, pressure, time, etc.
according to the production needs of different products, ensuring that the produced radiators have high and consistent quality and performance.
4, Safety and reliability:
The continuous brazing furnace adopts advanced safety protection measures, such as temperature protection and pressure protection, to ensure the safety and reliability of the production process.
Continuous furnace data
No. | ITEM | DATA |
1 | Nitrogen consumption | 60m³/h |
2 | Tunnel width | 1000mm |
3 | Tunnel height | 250mm |
4 | Drying temperature | 300 ℃ |
5 | Brazing temperature | 625℃ |
6 | Cooling method | air cooling |
7 | Solder flux | NOCOLOK |
8 | Heating method | electricity and natural gas |
9 | Delivery time | 95 days |
continuous brazing furnace control system
This control system is centrally controlled by an industrial computer, which can monitor temperature changes in real time,
automatically and unmanned control the entire heating process, intelligently control the atmosphere environment and many other advanced control capabilities
advantage
1, Automation control:
The control system of the continuous brazing furnace adopts advanced automation technology, which can achieve automatic control of key parameters such as temperature, pressure, and time
2, Accurate parameter settings:
Users can set parameters such as temperature, pressure, and time according to their actual needs to meet the application needs of different products.
3, Real-time monitoring:
It can monitor the operating status of equipment in real-time to ensure the safe and stable operation of the equipment.
4, Fault diagnosis and warning:
Able to timely detect equipment operation problems and provide warnings, helping users take timely maintenance measures
5, Friendly human-machine interface:
The control system is equipped with a friendly human-machine interface,
through which users can intuitively understand the operating status and parameter settings of the equipment, making it easy to operate and manage.
The control system of the continuous brazing furnace is the key to ensuring efficient and stable operation of the equipment.
It adopts advanced automation technology and precise parameter settings, supports real-time monitoring,
fault diagnosis, and early warning, and is equipped with a friendly human-machine interface, providing users with a convenient operation and management experience.