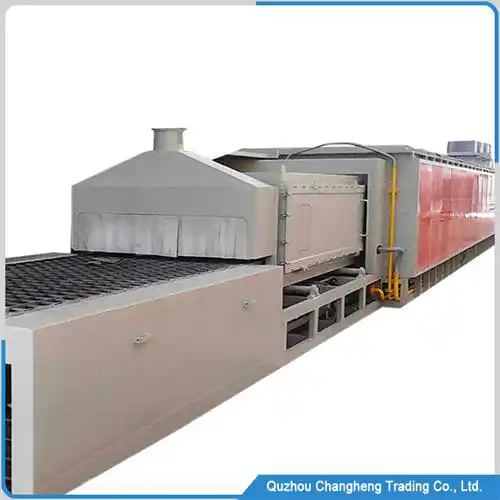
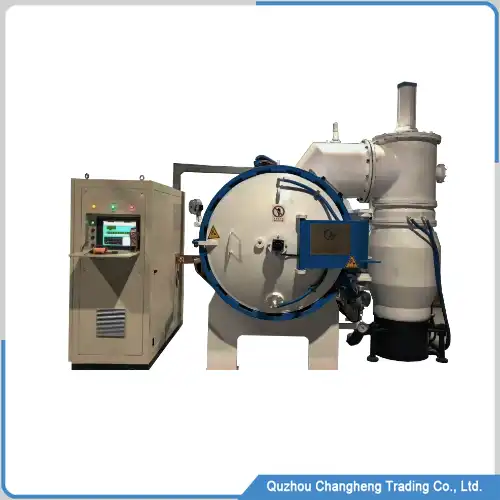
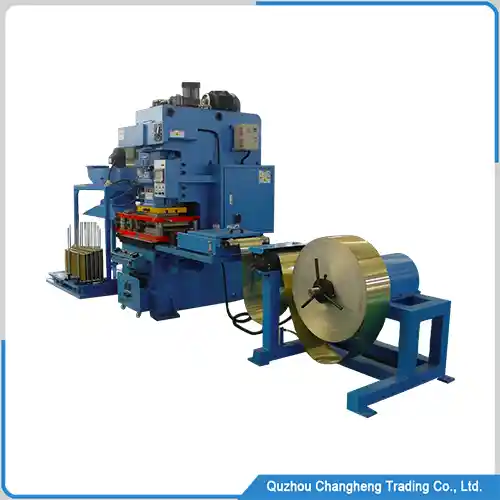
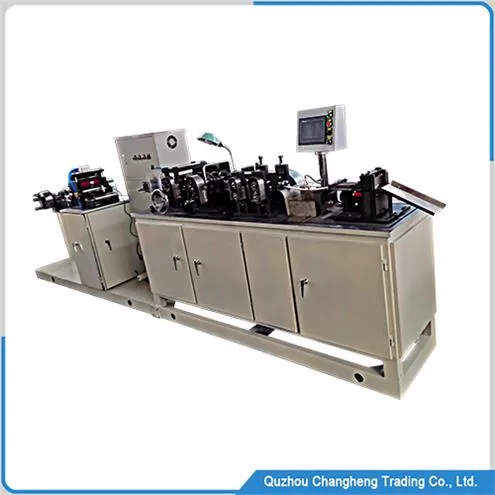
Machine Overview
This aluminum brazing furnace is a specialized equipment for brazing aluminum radiators. It is a continuous brazing production line in an atmosphere-protected environment.
This type of equipment has a wide range of applications and can be used for brazing various aluminum heat exchangers such as aluminum radiators, condensers, evaporators, intercoolers, oil coolers, etc.
With the continuous development of industry, electric cars have rapidly popularized people’s lives, and the battery cooling plates of these electric cars are also produced using this aluminum brazing furnace
During the aluminum brazing process, a layer of 4343 material on the surface of the aluminum material will melt, which comes into contact with another layer of aluminum material. After rapid cooling, the two are welded together,
This brazing process is carried out under the protection of the atmosphere, effectively preventing oxidation and corrosion, and ensuring the quality and strength of the weld.
aluminum brazing furnace data
No. | ITEM | DATA |
1 | Temperature | 0-720℃ |
2 | Thermocouple | Type K |
3 | Measurement accuracy | 2℃ or 0.2% |
4 | Heating rate | 80-120℃/h |
5 | Brazing technology | NOCOLOK |
6 | Cooling method | air cooling |
7 | Gas | Nitrogen |
aluminum brazing furnace production process
1, Degreasing
Before brazing, perform a degreasing treatment to remove oil and rust stains on the surface of the aluminum radiator, to ensure the smooth progress of the brazing process.
2, Flux Spray
After degreasing is completed, spray the brazing flux on the aluminum radiator and allow the brazing flux to fully penetrate the small pores of the aluminum radiator.
3, Drying
Dry the aluminum radiator that has undergone spray treatment to remove excess moisture and maintain thorough drying
4, Brazing
Place the dried aluminum radiator in a continuous aluminum brazing furnace with a protective atmosphere for brazing.
Under the protection of the atmosphere, all parts of the aluminum radiator are brazed at high temperatures
5, Cooling
After brazing is completed, the aluminum radiator is cooled to quickly cool down in a short time, forming a strong connection.
6, Forced cooling
Forced cooling of aluminum radiators to achieve the specified temperature range in a shorter time, facilitating worker operation
7, Completion
After the above steps, the operation process of the protective atmosphere continuous aluminum brazing furnace has been completed.
Workers need to place the welded aluminum core in the designated position
Aluminum brazing furnace working video
FAQ
A: Under normal circumstances, its delivery time is 95 days.
A: It is an innovative technology that saves 60% of ammonia compared to old machines, Only 50 cubic meters are needed per hour.
A: We have a solution to use natural gas heating to choose from.